SAT-TRAC–Part 7 Putting it together
Up to this point, everything worked as expected. That’s when you should expect the unexpected. First, one line of my relay control lines went low(shorted to ground) turning on one relay and starting to move the base around the tripod. When you have a 10 turn precision pot and you are operating in approx 3 to 6 turns, you have 4 to 7 turns either way to destroy it. Since it was the elevator motor silently turning, I didn’t catch it in time. That’s number 3 precision pot that I will replace. It’s down on the bottom, so I will need to take it apart to get to it. Not fun, but I got it done. So I think it’s a good idea to put a couple of Mechanical End of Travel rocker switches (EOT) to stop any runaway instances. I cut a couple of nylon standoffs and glued them to the 60 tooth gears for the Azimuth and Elevation mechanisms. The rockers will engage when they encounter the nylon bump. My thought was to shut the power down to the relays and motor speed controller if either AZ or EL reached its endpoint rather than rely on software to shut off the power which we will do too. Two ways to protect the unit is a good thing. Look into from top to see the end of travel for the azimuth in the center.
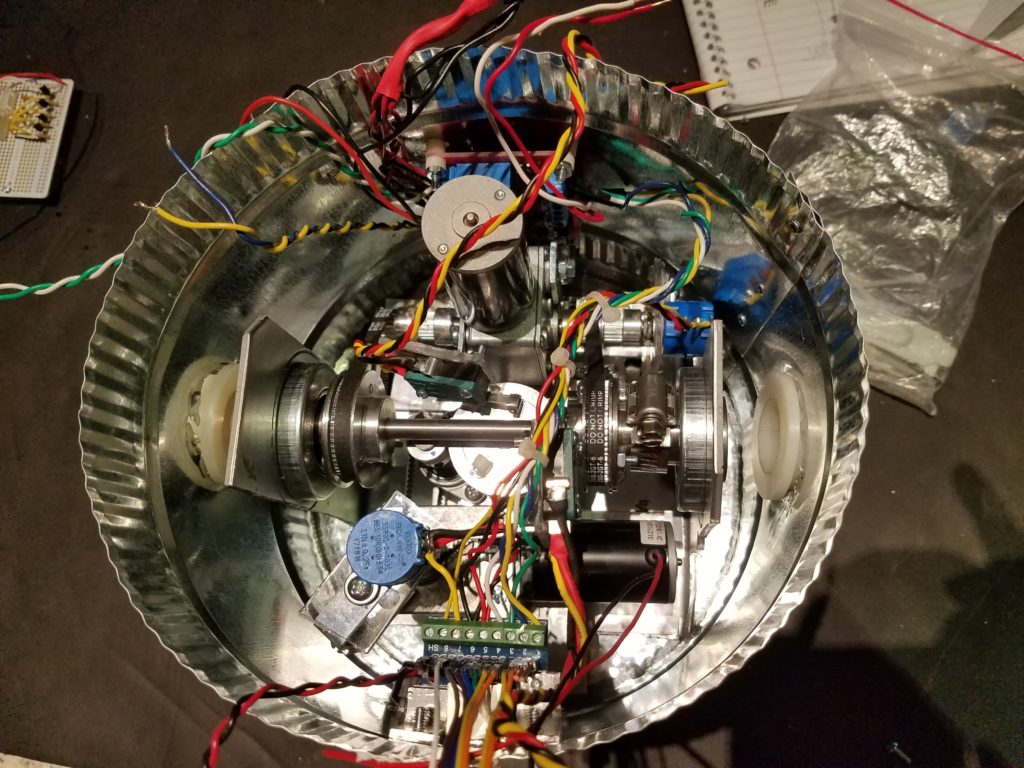
In the middle of the unit, you will see the Azimuth rocker switch that rotates around the stationary 60 tooth gear. Just to the right of it with the red/yellow/black wires is the stationary elevator rocker. If either switch is triggered, motors are off.
The elevator switch works great. However, my approach for Azimuth will require a different approach as it triggers at <0 and 340 degrees. I may need to narrow the speed bump to get closer to 360 degrees and possibly use an interrupt with a watchdog timer routine. Little detail that is important. So I’ll continue testing. Here is when you try to find something that you didn’t plan for. So I pull out the control line and 8V goes into some digital inputs… Ouch… Mega 2560 doesn’t like anything over 5.1V on most of its inputs. Next board. Jumping around with a VOM I found that the 5V reference source from the base, when I pull the plug the Mega 2560 was sinking juice from the 12V source. A 1n4004 blocked the current in this situation and everything worked. Test all of the possibilities before you are comfortable with its operation. I use an infrared temp gun to check for excessive heat on the FET’s, 2N3904’s, Mega 2560, and power supplies. Everything is reasonable <105F. Leaving it on for one week, sensor readings are stable and temps are consistent. It’s important that the current draw be monitored so you can observe any loading on the motors or any failure of the circuits. So far so good. What’s going to happen at -10F? Don’t know. How about +100F. Total meltdown? Anything is possible.
Here is the unit about 95% finished. The challenge with the AZ EOT is still being worked on. After getting it to a functional point, then the camera, antenna, servos, and fan can be hooked up on the top. Below is the top cap with a camera, 2 servos, and temperature controlled cooling fan. On the right is the control circuitry. The unit has been on for one week, its stable at 100ma draw at 12V. No smoke or excessive heat… All systems go…
2 servo 600 Line FPV camera TX operating at 5.9 Ghz with 200mw. Looking down the Sat-Trac – Testing the EOT switches